M6 Gewindeschneider: Ein umfassender Leitfaden
Der M6 Gewindeschneider ist ein wesentliches Werkzeug in der Metallbearbeitung, das zum Schneiden von Innengewinden der Größe M6 verwendet wird. In diesem Leitfaden erfahren Sie alles Wichtige über M6 Gewindeschneider, einschließlich ihrer Typen, Anwendung, Kaufkriterien und praktischen Tipps für die effektive Nutzung.
1. Was ist ein M6 Gewindeschneider?
1.1. Definition
Ein M6 Gewindeschneider ist ein Werkzeug, das verwendet wird, um Innengewinde mit einem Durchmesser von 6 Millimetern zu schneiden. Die Bezeichnung „M6“ steht für metrisches Gewinde mit einem Durchmesser von 6 mm. Gewindeschneider sind essenziell, um präzise Gewindebohrungen zu erstellen, die für die Aufnahme von M6 Schrauben oder Bolzen vorgesehen sind.
1.2. Typen von Gewindeschneidern
- Handgewindeschneider: Diese werden manuell verwendet und sind ideal für kleinere Serienfertigungen oder Einzelstücke.
- Maschinengewindeschneider: Für den Einsatz in Maschinen wie Drehbänken oder Fräsmaschinen konzipiert, ermöglichen sie eine schnellere und präzisere Bearbeitung großer Stückzahlen.
- Spiralgewindeschneider: Haben eine spezielle Spiralform, die das Abführen von Spänen erleichtert und die Reibung reduziert.
2. Anwendung des M6 Gewindeschneiders
2.1. Industriesektoren und Einsatzgebiete
- Maschinenbau: M6 Gewindeschneider werden häufig in Maschinen und mechanischen Geräten verwendet, um Teile präzise miteinander zu verbinden.
- Bauindustrie: Diese Gewindeschneider finden Anwendung bei der Befestigung von Konstruktionselementen, bei der Montage von Stahlkonstruktionen und in vielen anderen Bauanwendungen.
- Automobilindustrie: In Fahrzeugen werden M6 Gewindeschneider zur Herstellung von Gewindebohrungen in Motoren, Getrieben und anderen Komponenten eingesetzt.
2.2. Verbindungsarten
- Schrauben: M6 Schrauben werden für eine Vielzahl von Anwendungen verwendet, bei denen eine starke und zuverlässige Verbindung erforderlich ist.
- Bolzen: Diese werden oft zusammen mit Unterlegscheiben und Muttern eingesetzt, um stabile Verbindungen zu gewährleisten.
- Riegel und Stifte: In bestimmten Anwendungen, bei denen präzise Fixierungen notwendig sind.
3. Kaufkriterien für M6 Gewindeschneider
3.1. Material
- HSS (Hochgeschwindigkeitsstahl): Hochgeschwindigkeitsstahl-Gewindeschneider sind langlebig und vielseitig, geeignet für die meisten Metallarten.
- HSS-E (Hochgeschwindigkeitsstahl mit Kobalt): Diese bieten zusätzliche Härte und Wärmebeständigkeit und sind ideal für harte Materialien wie Edelstahl.
- Karbid: Karbid-Gewindeschneider sind extrem hart und langlebig, besonders für spezielle Materialien und Anwendungen geeignet.
3.2. Beschichtung
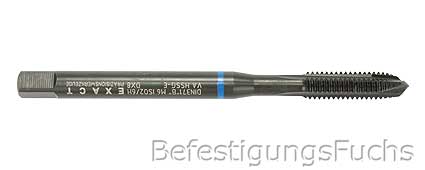
- Titanbeschichtung: Erhöht die Härte und Verschleißfestigkeit der Gewindeschneider und verbessert die Schneidleistung.
- Kobaltbeschichtung: Bietet zusätzliche Wärmebeständigkeit und ist für harte Materialien vorteilhaft.
3.3. Gewindetyp
- Metrisches Regelgewinde (M): Die Standardoption für M6 Gewindeschneider. Beachten Sie auch Feingewinde, z.B. M6x0,75.
3.4. Hersteller
- Qualität: Wählen Sie Gewindeschneider von renommierten Herstellern, um eine hohe Qualität und Langlebigkeit des Werkzeugs sicherzustellen.
4. Schritt-für-Schritt-Anleitung zum Schneiden eines M6 Gewindes
4.1. Vorbereitung
- Materialwahl: Verwenden Sie geeignete Materialien für das Werkstück, wie Stahl, Edelstahl oder Aluminium.
- Bohrloch vorbereiten: Bohren Sie ein Pilotloch mit einem Durchmesser von 5 mm, da das M6 Gewinde ein Lochdurchmesser von 6 mm benötigt.
4.2. Schneidvorgang
- Ausrichten: Setzen Sie den Gewindeschneider (M6) in das vorgebohrte Loch ein. Stellen Sie sicher, dass der Schneider senkrecht zum Werkstück steht, um ein gleichmäßiges Gewinde zu gewährleisten.
- Eindrehen: Drehen Sie den Gewindeschneider langsam und gleichmäßig in das Loch. Zu schnelles Arbeiten kann zu einem Werkzeugbruch oder einer fehlerhaften Gewindebildung führen. Verwenden Sie Schneidöl oder Schmiermittel zur Reduzierung der Reibung.
- Rückwärtsdrehen: Drehen Sie den Gewindeschneider regelmäßig leicht zurück, um Späne zu entfernen und ein Verstopfen des Werkzeugs zu verhindern.
4.3. Nachbearbeitung
- Reinigung: Entfernen Sie alle Späne aus dem Gewindeloch und reinigen Sie das Werkstück gründlich.
- Prüfung: Überprüfen Sie das geschnittene Gewinde mit einer passenden M6 Schraube oder einem Gewindelehrdorn, um sicherzustellen, dass das Gewinde korrekt geschnitten wurde.
5. Tipps zur Verwendung von M6 Gewindeschneidern
5.1. Auswahl des richtigen Werkzeugs
- Werkzeugqualität: Investieren Sie in hochwertige Gewindeschneider für eine bessere Leistung und Langlebigkeit.
- Werkzeugpflege: Halten Sie den Gewindeschneider sauber und in gutem Zustand, um eine lange Lebensdauer zu gewährleisten.
5.2. Schneidtechnik
- Gleichmäßiger Druck: Üben Sie gleichmäßigen Druck beim Schneiden aus, um ein gleichmäßiges Gewinde zu erhalten und das Werkzeug nicht zu überlasten.
- Vermeidung von Überhitzung: Schneiden Sie nicht zu schnell, um eine Überhitzung des Werkzeugs und des Werkstücks zu vermeiden.
5.3. Wartung und Pflege
- Reinigung: Entfernen Sie regelmäßig Späne und Rückstände von den Gewindeschneidern.
- Lagerung: Lagern Sie die Gewindeschneider an einem trockenen Ort und schützen Sie sie vor Beschädigungen.
6. Häufige Fragen
6.1. Wie erkenne ich, dass mein M6 Gewindeschneider stumpf ist?
- Antwort: Ein stumpfer Gewindeschneider kann Anzeichen wie ungleichmäßige Gewinde, Schwierigkeiten beim Schneiden oder Anhäufungen von Spänen aufweisen. Wenn das Schneiden schwieriger wird oder das Ergebnis ungenau ist, kann der Schneider stumpf sein.
6.2. Was soll ich tun, wenn das Gewinde nicht passt?
- Antwort: Überprüfen Sie die Größe des Pilotlochs und die Ausrichtung des Gewindeschneiders. Es könnte auch hilfreich sein, das Gewinde nachzuschneiden oder sicherzustellen, dass das Werkstück korrekt vorbereitet ist.
6.3. Kann ich M6 Gewindeschneider für alle Materialien verwenden?
- Antwort: M6 Gewindeschneider können in verschiedenen Materialien verwendet werden, darunter Stahl, Edelstahl und Aluminium. Achten Sie darauf, das richtige Material für Ihre Anwendung auszuwählen und gegebenenfalls spezielle Gewindeschneider für besonders harte Materialien zu verwenden.
Fazit
Der M6 Gewindeschneider ist ein vielseitiges und essentielles Werkzeug in der Metallbearbeitung, das für die Herstellung präziser Innengewinde verwendet wird. Durch das Verständnis der verschiedenen Typen, Materialien und Anwendungstechniken können Sie sicherstellen, dass Ihre Gewinde präzise und zuverlässig sind. Achten Sie auf die richtige Werkzeugwahl, Schneidtechnik und Pflege, um optimale Ergebnisse zu erzielen und die Lebensdauer Ihrer Werkzeuge zu maximieren.